A Comprehensive Approach to Dealing With Stretch Cover Machine Fixing Difficulties
You understand that stretch cover makers are critical for maintaining effectiveness in packaging operations. Concerns can develop that interfere with performance. What are the ideal approaches to guarantee your devices run smoothly?
Understanding Typical Stretch Wrap Device Issues
When you depend on stretch wrap devices for efficient product packaging, it's vital to identify typical issues that can disrupt procedures - stretch wrap machine repair. One common problem is inconsistent stress, which can cause insufficient wrapping and endangered lots stability. If you see the movie isn't sticking correctly, look for damaged rollers or incorrect setups
Another issue you could encounter is film damage, typically triggered by wrong movie kind or maker breakdowns. On a regular basis inspect the maker for indications of wear and tear to avoid this.
In addition, keep an eye on film buildup or jams, which can halt production. Frequently, this occurs as a result of imbalance or debris in the equipment.
Finally, improper sealing can result in lots splitting up during transportation. Make particular your device is adjusted properly to maintain the stability of your packages. By remaining alert and dealing with these concerns quickly, you can promote smoother operations.
The Relevance of Routine Preventive Upkeep
Regular precautionary upkeep is important for maintaining your stretch wrap machine running efficiently and effectively. By consistently checking and servicing your devices, you can detect prospective concerns prior to they escalate into pricey repair work. This positive approach not only expands the lifespan of your maker but likewise assures that it runs at peak efficiency.
You need to schedule regular assessments to tidy, lubricate, and replace worn parts. Maintaining your device calibrated assists maintain optimal covering quality, lowers waste, and improves efficiency. In addition, recording maintenance tasks develops a reputable background that can educate future choices.
Don't overlook the significance of training your personnel on upkeep ideal techniques. When everyone understands just how to care for the device, you lessen the threat of driver mistake bring about break downs. Simply put, devoting to regular preventive upkeep is a clever financial investment that repays in reduced downtime and enhanced performance in your operations.
Troubleshooting Techniques for Quick Repairs
Efficient troubleshooting techniques can substantially reduce downtime when your stretch wrap equipment runs into issues. Is the machine not wrapping correctly or is it making unusual noises?
Following, examine the equipment's setups and controls; occasionally, a simple change can solve the issue. Check the film tension and positioning, as inappropriate setup can cause wrapping failings. Do not ignore electrical connections; loosened or broken cords can interfere with capability.
If you're still facing obstacles, take into consideration running analysis tests if your machine has that capacity. Don't think twice to seek advice from with a service technician if you can not resolve the concern rapidly.
Training Operators for Effective Maker Use
To assure your stretch wrap device operates at peak efficiency, proper training for operators is necessary. When drivers understand the device's functionalities, they can maximize its potential and minimize downtime. Beginning by providing them with detailed manuals that lay out operational procedures and safety protocols. Hands-on training is important; it enables operators to familiarize themselves with the equipment's controls and settings.
Urge them to exercise under guidance, dealing with any concerns or concerns they could have. On a regular basis set up refresher courses can keep their skills sharp and help them adjust to any type of updates or modifications in technology.
Additionally, infuse a culture of accountability by encouraging drivers to report issues or recommend renovations. This positive approach not just improves their confidence however also adds to the general efficiency of your procedures. With well-trained operators, you'll see less errors and raised efficiency, ensuring your stretch cover machine continues to be an important asset.
Developing a Strong Interaction Channel In Between Teams
Well-trained drivers can just do at their best when there's a strong communication network between groups. Effective interaction eliminates misconceptions and guarantees every person's on the same web page concerning equipment operations and fixing needs. Urge regular check-ins and conferences to discuss concerns, share understandings, and address issues.
Making use of innovation, like messaging applications or collaborative platforms, can boost real-time communication, making it much easier to report problems and share updates quickly. Designating clear functions and responsibilities promotes liability, allowing staff member to get to out to the that site right person when concerns develop.
Moreover, creating an open atmosphere where every person really feels comfy sharing feedback can result in ingenious remedies. By focusing on communication, you're not just improving device efficiency; you're likewise constructing a natural group that interacts seamlessly. This collaborative spirit eventually results in quicker repair services and lowered downtime, profiting the whole procedure.
Purchasing Top Quality Substitute Components
When it involves keeping your stretch cover equipments, spending in top quality substitute components is crucial for making certain reliable performance and minimizing downtime. Cheap alternatives might appear alluring, however they typically cause even more significant problems down the line, costing you a lot more out of commission and shed productivity. By choosing top notch components, you're not just repairing a problem; you're boosting the total effectiveness of your equipment.
Additionally, top quality components are usually manufactured to more stringent requirements, which implies they'll fit better and operate even more reliably. This lowers the probability of unforeseen breakdowns, permitting your operations to run smoothly. Furthermore, reliable distributors commonly offer service warranties, providing you comfort in your financial investment.
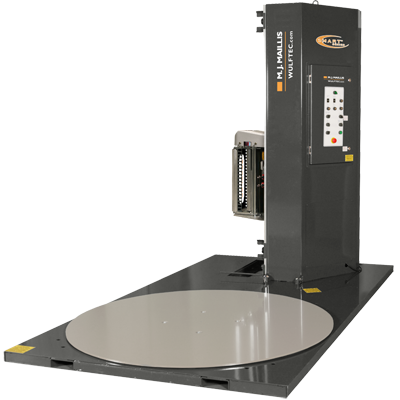
Analyzing Performance Data for Constant Improvement
To boost your stretch wrap maker's efficiency, you need effective data collection techniques. By examining efficiency metrics, you can identify locations for improvement and improve performance. Recognizing these opportunities not only streamlines operations but likewise lowers downtime and repair work expenses.
Information Collection Methods

Performance Metrics Assessment
While assessing efficiency metrics, it's vital to concentrate on details data factors that directly affect your stretch wrap device's effectiveness. Beginning by tracking cycle times, as they expose just how rapidly your maker runs under regular problems. Display downtime incidents to determine patterns or recurring problems that might need attending to. Maintain an eye on movie use, guaranteeing you're not losing product, which can influence prices and efficiency. Furthermore, examine result quality by examining for incongruities in the wrapping process. By examining these metrics on a regular basis, you can determine locations requiring attention and take positive procedures. This constant analysis aids boost productivity, lower prices, and ultimately enhance your equipment's longevity, leading to an extra reliable wrapping operation in general.
Identifying Renovation Opportunities
As you assess efficiency information, you can reveal valuable enhancement opportunities that boost your stretch cover device's performance. Look for trends in downtime, cycle times, and cover quality. If regular failures correlate with specific operating conditions, you can change processes to alleviate these concerns.
Often Asked Inquiries
How Can I Tell if My Equipment Needs a Repair Work or Just Maintenance?
To tell if your device needs repair service or simply maintenance, pay attention for uncommon noises, check for inconsistent performance, and examine for visible wear. If issues persist after maintenance, it's most likely time for a repair.
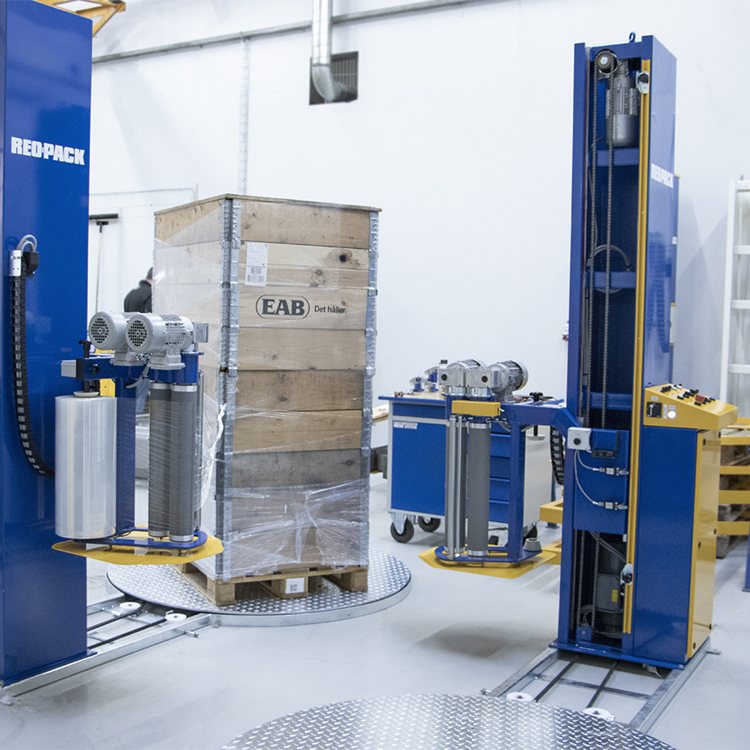
What Is the Average Life-span of a Stretch Cover Device?
The average life-span of a stretch wrap equipment is usually 5 to ten years, relying on usage and upkeep. Routine care can extend its life, so watch on efficiency and address issues without delay.
Exist Particular Brand Names Understood for Better Reliability?
Yes, some brand names are known for their dependability. You'll locate that business like Signode and Lantech frequently obtain positive reviews - stretch wrap machine repair. Looking into customer comments can help you address select a reputable stretch wrap maker for your demands
What Are the Signs of Poor Driver Training?
If you notice constant errors, inconsistent wrapping, or safety and security cases, those are signs of bad driver training. Absence of recognizing about maker features or failing to follow methods can considerably influence effectiveness and safety.
Just How Can I Discover a Professional Specialist for Services?
To find a qualified service technician for repair work, ask for referrals from market peers, examine on the internet testimonials, and verify qualifications. You might also think about speaking to local devices suppliers who usually have relied on technicians accessible.
Final thought
To sum up, taking on stretch wrap equipment repair service challenges requires a proactive technique. Do not forget the significance of strong communication between teams and continuous evaluation of machine output.